Outsource your Supply Chain Control Tower to a 4PL?
- Rob van Doesburg
- Mar 24, 2022
- 1 min read
Shippers use Supply Chain Control Towers to orchestrate and improve their supply chain. A Control Tower can be insourced and operated by the SC organisation of the shipper, can be outsourced to a 4PL or a hybrid set-up can be implemented. How to decide which solution best fits your objectives and requirements?
For designing, implementing and running SC Control Towers the following capabilities are needed:
Best-practice processes for each control tower function like network design, procurement, planning, execution management, finance and analysis/reporting
Capable staff like planners, customer service employees, controllers, carrier managers, engineers and analysts to conduct planning, execution and optimisation tasks
State-of-the art technology to support the control tower functions with OMS, TMS, BI and/or sourcing systems and tools
Project and change management expertise to design, implement and optimise the control tower solution
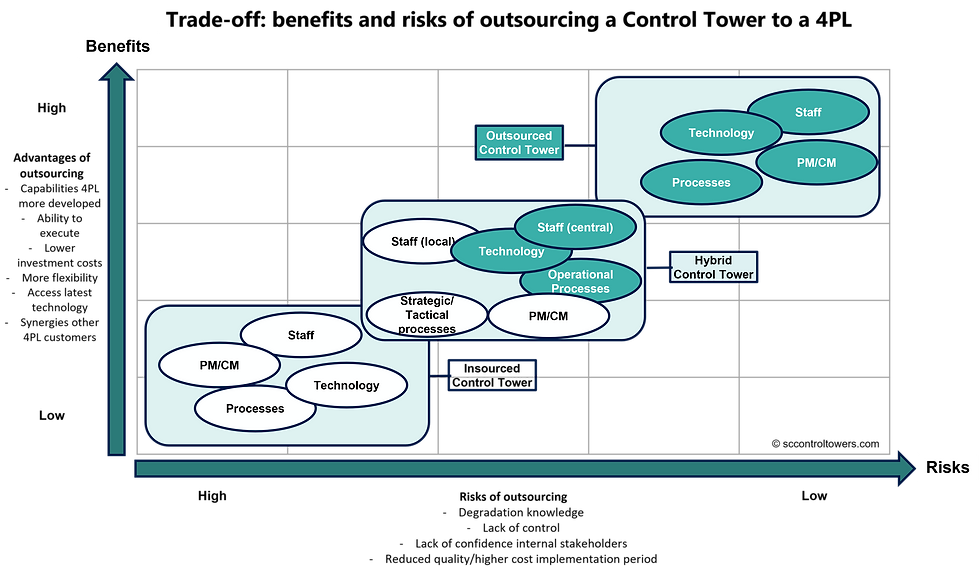
The decision to outsource a SC Control Tower will be the outcome of a trade-off between the advantages of outsourcing and the related risks as illustrated in the graph above. The outcome could well be a hybrid model were for example the operational processes and supporting technology are outsourced and strategic/tactical processes and local staff tasks are kept in-house. The outcome of this decision also depends of course on the complexity of the supply chain and maturity of the current supply chain organisation. For this reason, the decision should be made for each region and supply chain function (sourcing, delivery and service) separately.
The knowledge platform www.sccontroltowers.com provides more information on SC Control Tower solutions in general and an overview and the main characteristics of 4PL providers: https://www.sccontroltowers.com/overview-4pl-providers.
Comments